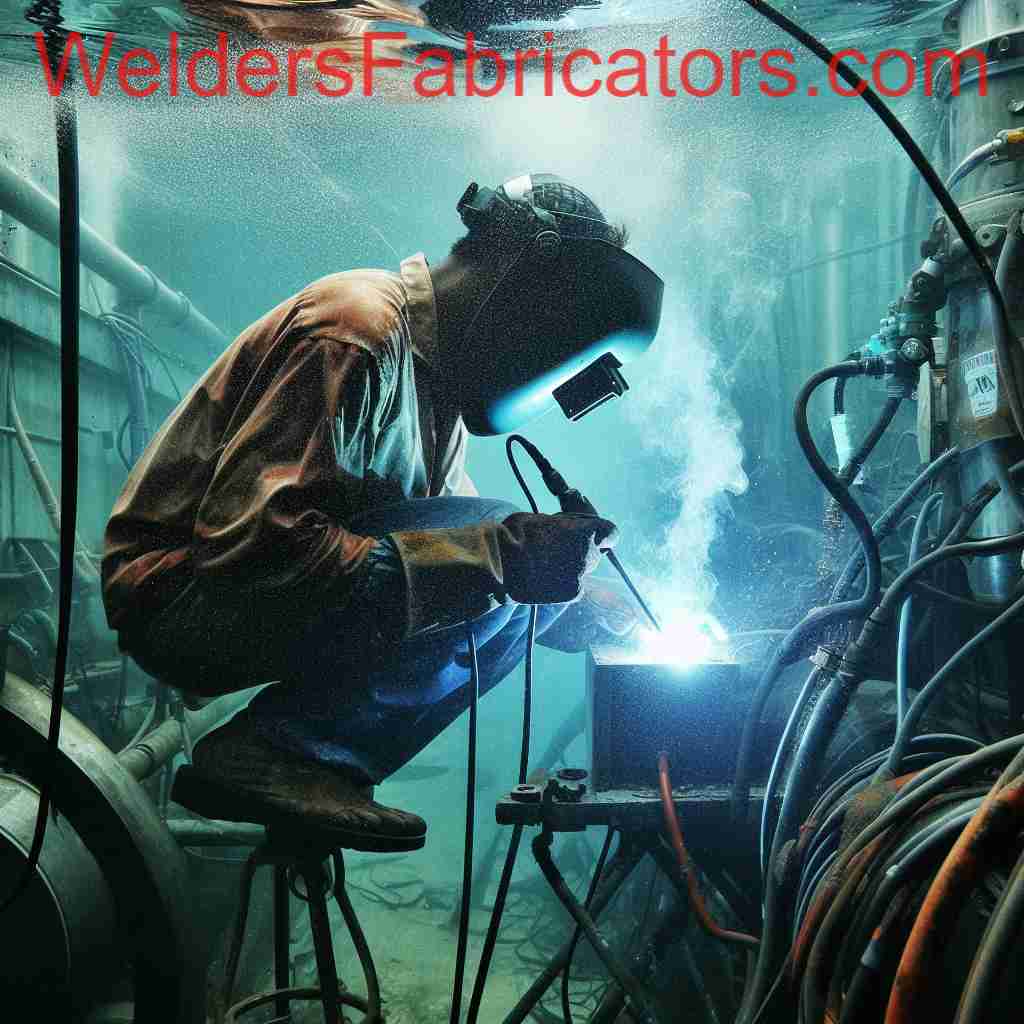
The welding industry thrives on creative fire and molten metal, but amidst the sparks and fumes lies a labyrinth of regulations and safety protocols. For welding professionals and business owners, navigating this complex landscape can feel like defusing a live wire blindfolded. However, fret not, intrepid welders, for this guide illuminates the path to compliant operations, ensuring your workshop hums with productivity and peace of mind.
Charting the Course:
- Know Your Regulatory Landscape: Regulations can differ by region, country, and type of welding. Familiarize yourself with the relevant bodies governing your operations, such as OSHA in the US or the European Union’s Welding Equipment Directive.
- Decoding the Standards: Dive into the specific standards applicable to your work. Popular standards include AWS (American Welding Society) and ISO (International Organization for Standardization). These standards set guidelines for welding procedures, equipment, and qualifications.
- Chart Your Risk Assessment: Every welding project possesses unique hazards. Conduct thorough risk assessments before starting work, identifying potential dangers and implementing appropriate control measures.
- Invest in Training: Knowledge is your shield. Ensure your team undergoes proper training on safety procedures, specific welding techniques, and relevant standards. Refresher courses keep minds sharp and skills honed.
Building a Fortress of Safety:
- Equipment Essentials: Equip your workshop with certified welding equipment in good working condition. Regular maintenance and inspections prevent accidents and maintain optimal performance.
- Personal Protective Armament: Gear up! Provide your team with the right personal protective equipment (PPE) for their tasks, including helmets, gloves, respiratory protection, and fire-resistant clothing.
- The Power of Labels: Label all hazardous materials and welding gases clearly and accurately. This small step can prevent confusion and potential disasters.
- The Emergency Arsenal: Be prepared for the unexpected. Ensure your workshop has readily available fire extinguishers, first-aid kits, and emergency procedures in place.
Maintaining Constant Vigilance:
- Documentation is Key: Maintain thorough records of welding procedures, training certificates, and risk assessments. This documentation safeguards your business and demonstrates compliance in case of inspections.
- Embrace Audits: Don’t shy away from internal and external audits. These examinations identify potential discrepancies and offer valuable feedback for improving your safety culture.
- Communication is Your Lifeline: Foster open communication between management and workers. Encourage reporting of near misses and safety concerns to proactively address hazards before they escalate.
- Continual Improvement: Safety is a journey, not a destination. Strive for continuous improvement by proactively researching new safety technologies, attending industry seminars, and staying updated on evolving regulations.
Remember, navigating regulations and safety compliance isn’t just about ticking boxes – it’s about safeguarding your team, protecting your business, and creating a healthy work environment where creativity can truly flourish. By embracing these practices, you transform your welding shop from a potential hazard zone into a beacon of safety and efficiency, where the only sparks that fly are those born from passion and skill. So, wield your knowledge as your torch, illuminate the path to compliance, and build a future where safety fuels your success.
Are you a welding warrior, a master of metal, a sculptor of sparks? Do you crave the thrill of molten steel and the satisfaction of a job well done? Then stop wandering the industrial wasteland, your perfect flame awaits on WeldersFabricators, the job portal forged for passionate professionals like you.