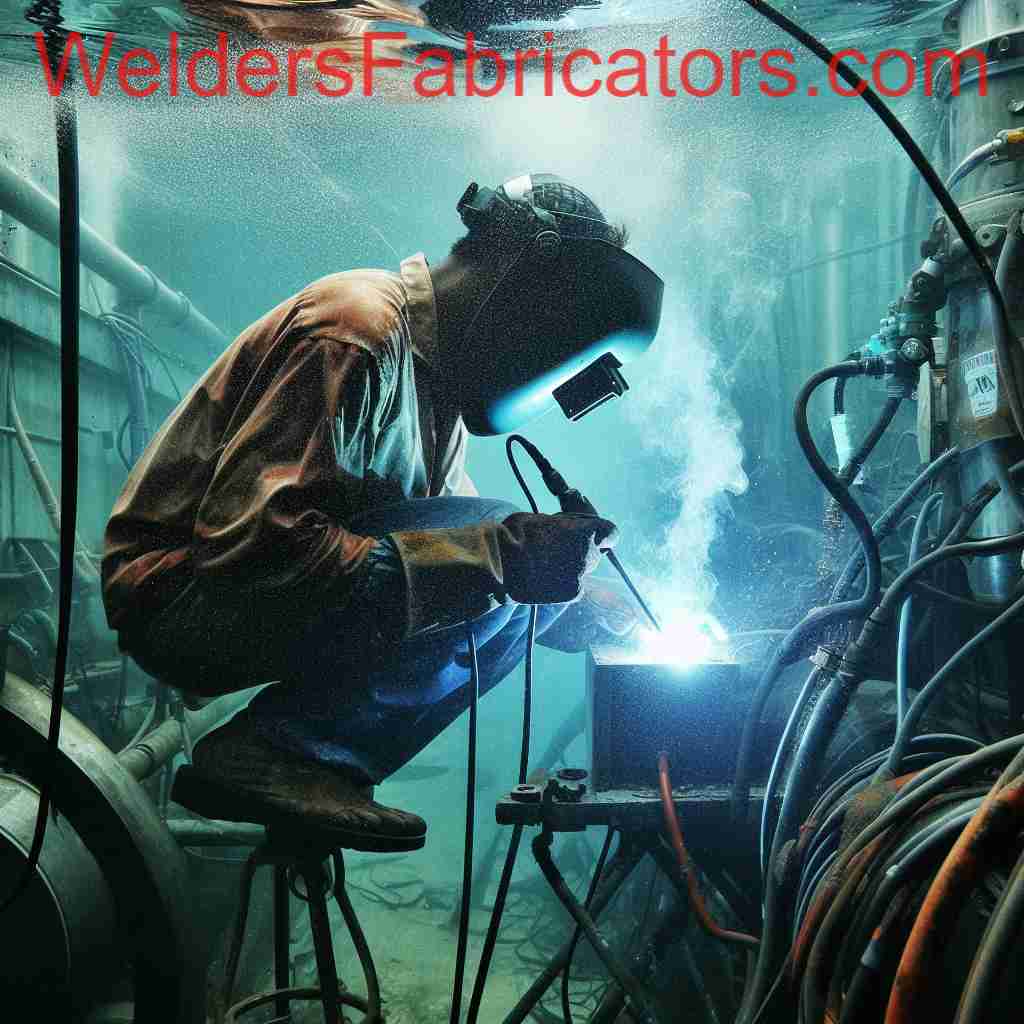
In today’s globalized world, the question of outsourcing welding and fabrication work looms large for many companies. It’s a decision loaded with potential for both advantages and disadvantages, carefully balanced on the scales of cost, quality, control, and risk. So, before you hand your blueprints off to an unknown forge across the ocean, let’s ignite the discussion and explore both sides of the fiery coin.
Advantages of Outsourcing:
- Cost savings: This is often the siren song of outsourcing. Lower labor costs in some countries can significantly reduce your production expenses, potentially boosting your bottom line and making your products more competitive.
- Access to skilled labor: If you struggle to find skilled welders and fabricators locally, outsourcing opens doors to a potentially larger pool of talent. This can be particularly beneficial for specialized welding techniques or niche projects.
- Focus on core competencies: Outsourcing non-core functions like welding can free up your internal resources to focus on your strengths, like design, marketing, or sales. This can lead to greater efficiency and strategic focus.
- Global reach: Outsourcing can help you tap into new markets and expand your reach without the need for physical expansion. This can be a great way to grow your business internationally.
- Innovation and knowledge sharing: Working with international partners can expose you to new technologies, techniques, and best practices. This cross-cultural exchange can foster innovation and improve your overall production quality.
Disadvantages of Outsourcing:
- Quality control: Maintaining quality control can be challenging when working with faraway partners. Language barriers, cultural differences, and varying safety standards can pose risks to production quality and your brand reputation.
- Communication and collaboration: Effective communication and collaboration are crucial for successful outsourcing. Time zone differences, language barriers, and cultural nuances can make working seamlessly with remote teams a complex task.
- Intellectual property protection: Sharing sensitive designs and technical specifications with overseas partners carries the risk of intellectual property theft and unauthorized manufacturing. Protecting your IP becomes a critical concern.
- Logistical challenges: Shipping raw materials and finished products across borders can be complex and expensive. Delays, customs issues, and transportation costs can eat into your potential cost savings.
- Loss of control: Outsourcing involves relinquishing some control over your production process. This can be uncomfortable for some companies, especially when quality, safety, and compliance are paramount.
Ultimately, the decision to outsource welding and fabrication work is a complex one, with no one-size-fits-all answer. It’s crucial to carefully weigh the potential advantages and disadvantages in the context of your specific business needs, resources, and risk tolerance.
Consider conducting thorough due diligence on potential partners, establishing clear communication channels and quality control protocols, and securing your intellectual property before stepping onto the global forge. Remember, successful outsourcing is not simply about finding the cheapest labor, but about building strong, reliable partnerships that can truly fuel your business growth.
So, ignite your analysis, weigh the fire of opportunity against the risks of compromise, and forge your own path in the international furnace of welding and fabrication. Just remember, like any powerful tool, outsourcing can be a double-edged sword – wield it wisely to forge your future success.